Ensuring success of manufacturing projects: a guide to smart simulation & planning
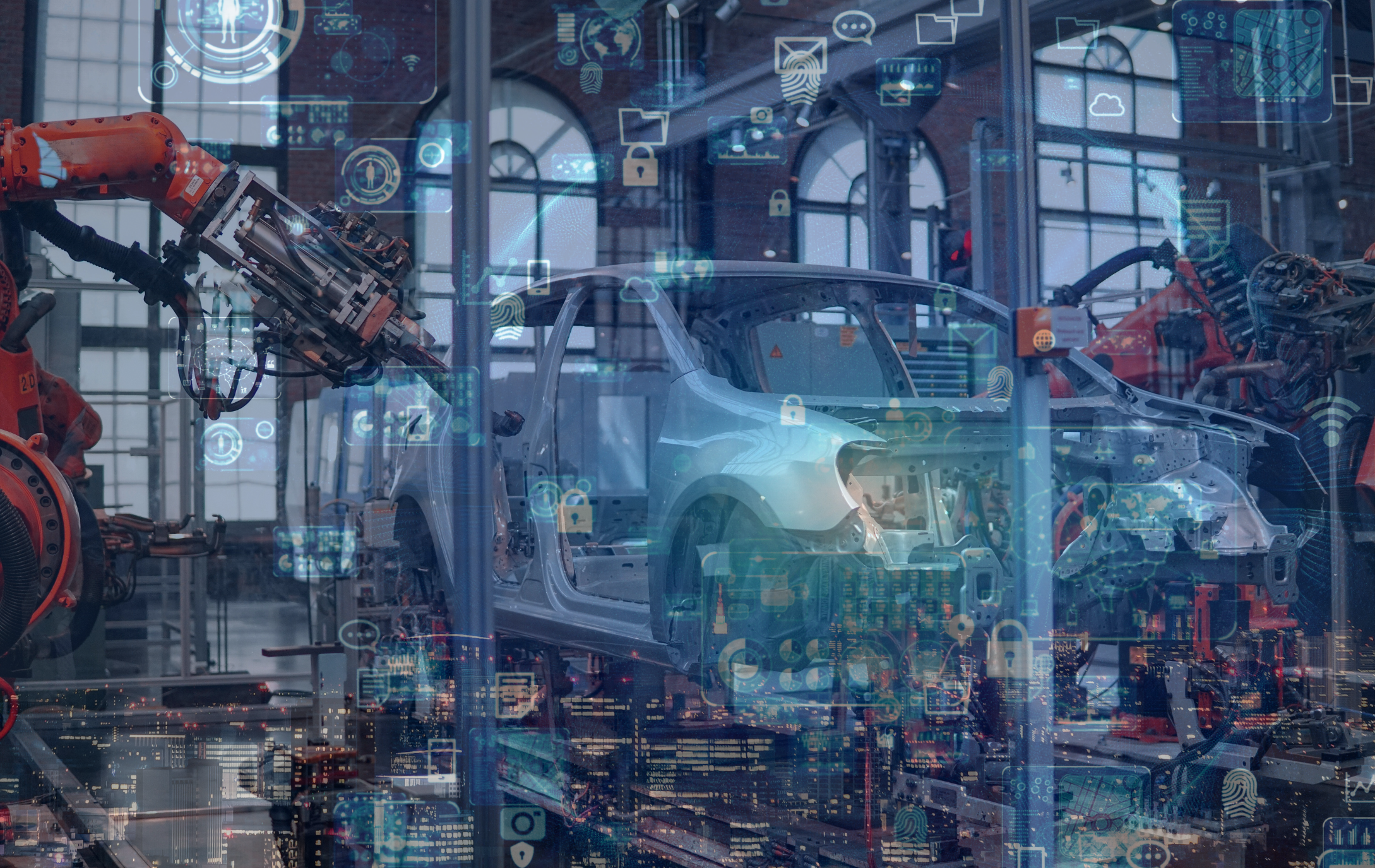
Imagine a world where every manufacturing project unrolls with precision, where production lines vibrate in harmonious perfection and last-minute chaos is a relic of the past. This is not an episode out of some sci-fi movie, but the realistic outcome achievable today through meticulous planning and cutting-edge simulation technologies. Here, in this short guide to ensuring the success of manufacturing projects through smart simulation and planning, we explore how these elements are the backbone of successful manufacturing projects from automotive to electronics and many others.
Projects aren’t successful by mere chance but are engineered to succeed right from the start. Let’s delve into the strategic planning and advanced simulations that pave the way for a seamless, error-free production process—surpassing current standards of manufacturing excellence.
The Critical Role of Planning
At the heart of any successful manufacturing project lies a well-thought-out planning phase. This phase is the blueprint from which all manufacturing strategies are developed. Planning includes an analysis of the requirements of the project, allocation of resources, assessment of potential risks, and setting up the timeline. Perfect planning makes sure it is protected from any kind of possible fail and assures smoothness and effectiveness in operating the project.
Key Planning Strategies:
- Resource Allocation: Proper allocation of resources, including manpower, materials, and machinery, ensures that projects are not delayed due to shortages.
- Risk Management: Identifying potential risks and developing mitigation strategies can prevent costly setbacks.
- Timeline Scheduling: Detailed schedules help coordinate various project phases, ensuring that each segment progresses without delay.
Manufacturing Simulation: A Game-Changer
Manufacturing simulation is a game-changing tool in industrial operations. It provides a virtual model of the production process, which allows the visualization, analysis, and optimization by engineers and project managers of the workflow without developing a physical proof and without the need for trial and error
How Does Manufacturing Simulation Work?
Manufacturing simulation consists of a precise digital replication of the manufacturing process down to the machinist operations, worker actions, and product assembly lines. This simulation allows for:
- Visualization: Teams can see the manufacturing process in action before it is implemented, helping to identify any potential issues in workflow or design.
- Optimization: It provides data on process efficiency, allowing managers to tweak and optimize various elements such as machine placement and operational sequences.
- Validation: Simulation validates the manufacturing process against the designed parameters, ensuring that the system operates as intended before full-scale production begins.
Benefits of Manufacturing Simulation:
- Reduced Time to Market: Accelerates the design and development phases, allowing for quicker project completion.
- Cost Efficiency: Identifies costly errors in the planning phase, reducing the potential for expensive corrections during physical implementation.
- Enhanced Product Quality: Ensures product quality by allowing for adjustments and optimizations before the manufacturing process begins.
Integration with Industry 4.0 and Beyond
Especially in the context of Industry 4.0, where digitization and interconnectivity of factories are the main intentions, manufacturing simulation is a matter of fact necessity. Therefore, other Industry 4.0 technologies of IoT devices designed to improve informed decision making and efficient operations with advanced analytics work perfectly with simulation tools.
Future Trends:
- Industry 5.0: As we move towards Industry 5.0, the role of simulation will expand to include more human-centric approaches, focusing on customizations and enhancements in human-machine interactions.
- AI Integration: Artificial intelligence can further enhance manufacturing simulations with predictive analytics and more advanced decision-support systems.
Case Studies and Success Stories
Manufacturing simulations have already proven their value in several industries. In its elbow-to-elbow experience with major Italian industrial companies, Flexcon has often come across excellent examples. For instance, an automotive company that used simulation to optimize the screw tightening process in assembly lines, achieving consistent cycle times and increased productivity. Another example is a large food packaging company that used simulation to automate and refine its palletizing process, dramatically reducing cycle times from minutes to seconds, and being able to simulate its packaging lines to potential buyers of its systems. Stay tuned to learn about Flexcon‘s top business cases for success.
The success of a manufacturing project must be optimized not only with quality raw materials and machinery, but also by reaching the point of operation through strategic planning and simulations. Manufacturing simulation, endorsed by manufacturers, makes it possible to predict probable problems, optimize the process and increase the level of productivity, thus making manufacturing projects a success. This area, with the development of digital technologies, will increase its impact in the near future to become an essential tool for the manufacturing industry.
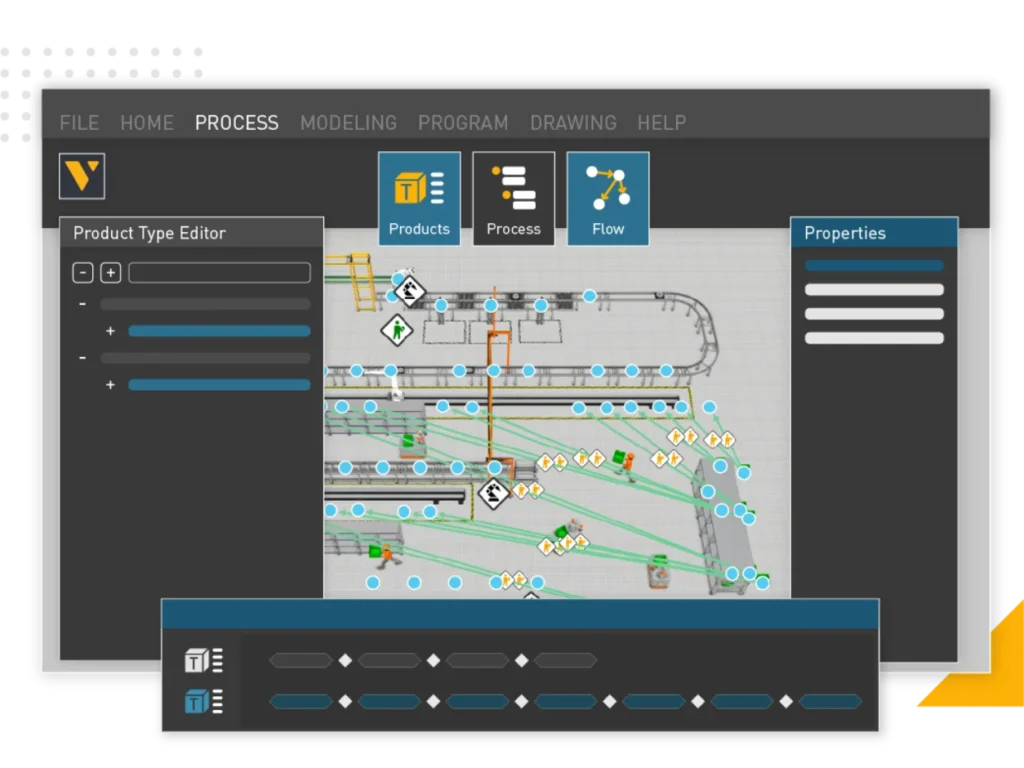
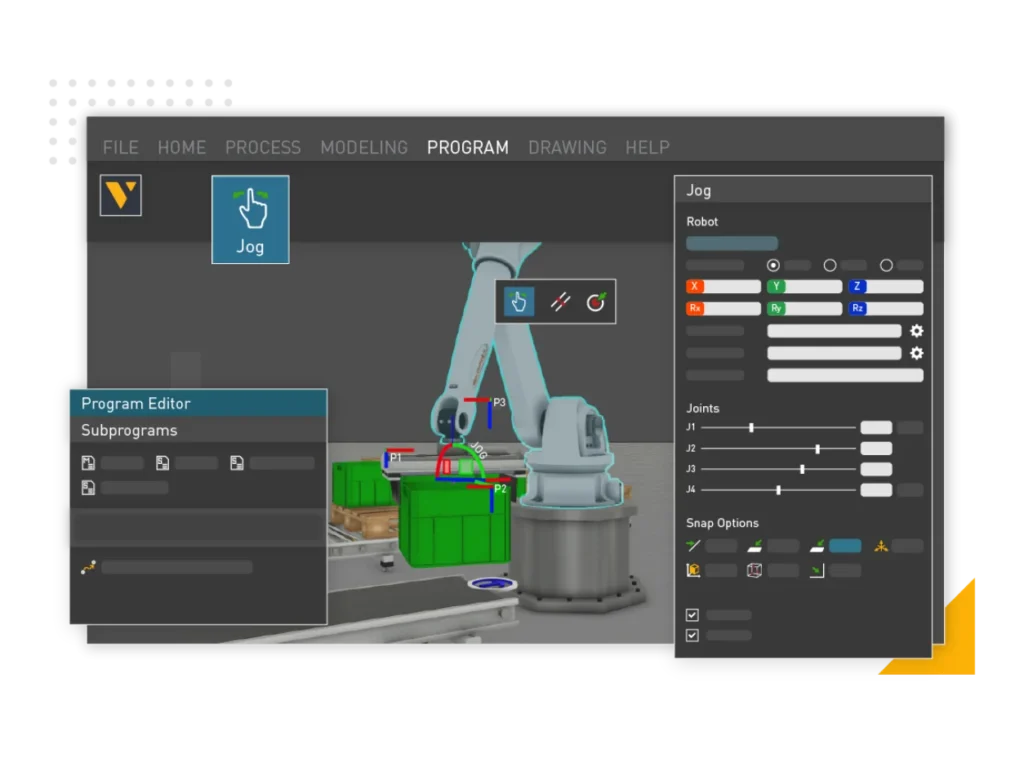
Best practices for effective manufacturing simulations
Integrating simulation into the manufacturing process is a critical step for optimizing both existing and new production workflows. It demands significant technological investment, but the benefits in operational cost reductions, organizational efficiency, and training are profound.
Here we outline some of the best practices derived from extensive industry experience in dynamic production simulations:
1. Clearly define objectives and problems
Before diving into the simulation, it’s essential to define what you aim to achieve and the specific problems you’re addressing. Whether it’s reducing cycle time, minimizing resource wastage, or streamlining logistics, a clear set of objectives guides the simulation process effectively.
2. Develop a conceptual model
Construct a conceptual model that simplifies the real-world process into manageable elements. This model serves as the blueprint upon which the entire simulation is built. It should capture the essential components of the manufacturing process, including workflow, resources, and interactions.
3. Validate the conceptual model
Validation ensures that the model accurately reflects the physical process it represents. This step is crucial for building credibility in the simulation results and should involve checking for logical correctness and verisimilitude with actual production scenarios.
4. Collect and analyze input data
The quality of a simulation is highly dependent on the input data. Collect precise and comprehensive data about the production environment, including machine capabilities, worker efficiency, and material properties. This data must be analyzed to ensure it supports the objectives identified in the first step.
5. Translate into a mathematical model
Transform the conceptual model into a mathematical framework that can be simulated. This step involves defining mathematical relationships between different elements of the process, incorporating stochastic parameters to account for variability and uncertainty in production.
6. Calibration and validation
Once the mathematical model is established, it must be calibrated to reflect real-world conditions accurately. This might involve adjusting the model parameters based on historical data and validating the model by comparing its output against known data.
7. Design and execute simulation experiments
Plan and carry out a series of simulation experiments. This involves setting up different scenarios to test hypotheses about improvements and adjustments in the production process. Each scenario should be designed to yield insights that can lead directly to actionable improvements.
8. Analyze output data
Finally, analyze the data generated by the simulations to assess performance under various conditions. This analysis will reveal strengths and weaknesses in the process, guiding further tweaks and improvements.
9. Implementation of results
Translate the successful simulation scenarios into real-world applications. Implement the changes in the manufacturing process as identified through the simulation to realize improvements in productivity, quality, and cost-efficiency.
Tools and technologies
Utilize advanced simulation software and technologies such as FlexSim and Visual Components which offer robust environments for experimentation, analysis, and visualization. These tools can handle complex simulations, including those involving digital twins and cyber-physical systems, which are crucial for integrating Internet of Things (IoT) technologies.
By adhering to these best practices, manufacturers can leverage simulations to predict outcomes, plan effectively, and execute manufacturing processes that meet the modern demands of speed, efficiency, and adaptability. This proactive approach is vital in an era where production complexity and technological integration are ever-increasing.
From macro to micro
In simulating an entire factory or industrial process, it is necessary to always move from imagining first the strategy, then the tactics: that is, first the global and macro-level operations, and only then the intricate and micro-level details. This step is critical because it allows manufacturers not only to visualize the entire production line in broad strokes, but also to zoom in on specific components and interactions, without losing sight of their focus.
Reconciling a view of the process as a whole with a granular focus helps identify inefficiencies and potential failures at the smallest levels, which are often the catalysts for broader operational challenges.
Visual Components is an advanced simulation software that expertly navigates the transition from macro to micro perspectives in industrial processes. At the macro level, it enables users to model and visualize entire production workflows, providing a broad overview of operations and allowing for strategic planning and optimization. This includes layout configuration and throughput analysis, essential for understanding how different parts of the system interact and influence overall productivity.
On the micro scale, Visual Components delves into the detailed 3D modeling and simulation of specific pieces of machinery, such as robots. It offers tools to simulate the individual functions and movements of these machines within the production line. This level of detail is crucial for troubleshooting specific operational issues, optimizing machine performance, and ensuring seamless integration into the wider workflow. By bridging the gap between large-scale process management and fine-grained mechanical simulations, Visual Components provides a comprehensive toolset that enhances both the design and execution of industrial operations.
Contact Flexcon: discover how to test and refine your real production strategies in a virtual environment.