Ergonomics with Visual Components 4.9 and RULA
The integration of Visual Components 4.9 with the RULA component simplifies ergonomic assessment, optimizing human-machine collaboration and enhancing operator well-being.
In recent years, industrial production has undergone a profound transformation. This has prompted reflection on the role of the individual in the factory of the future. Initially, Industry 4.0 suggested that automation and digitization could replace much of human labor.
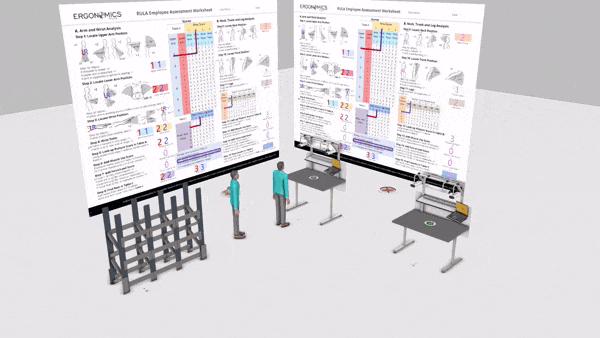
With the rise of Industry 5.0, it has become clear that individuals are irreplaceable due to their unique capabilities, such as intuition, strategic vision and understanding of physical space and systems.
Thus, it is the transition from Industry 4.0 to Industry 5.0 that highlights how human labour remains essential in production, due to the ability to interpret malfunctions, solve problems and grasp the subtleties of production workflows. Even for the most practical tasks, while machines and cobots (collaborative robots) can support or replace operators, human involvement remains crucial. This is because human expertise and adaptability allow unforeseen situations to be handled and operations to be optimised in real time.
In this context, ergonomics becomes crucial. Alongside the pursuit of sustainability, Industry 5.0 focuses on designing production lines by measuring the impact of gestures, movements and rhythms on the performance of operators working in highly automated environments. The aim is not only to achieve maximum efficiency, but also to ensure people’s health and safety.
RULA and Visual Components: ergonomics for the future of manufacturing
The RULA (Rapid Upper Limb Assessment) module integrated into Visual Components 4.9 is based on the method developed by Lynn McAtamney and E. Nigel Corlett in 1993 at the University of Nottingham. This method is described in the publication “RULA: A Survey Method for the Investigation of Work-Related Upper Limb Disorders”. It was designed to assess ergonomic risks linked to upper limb disorders. By evaluating posture, force, and repetitive movements, it helps identify corrective actions to reduce workplace risk factors.
In the context of Visual Components‘ 3D simulation, this tool allows you to:
- Visualize and assess ergonomic risks directly within simulations.
- Capture body postures, forces, and repetitive movements, identifying critical areas.
- Score postures to pinpoint necessary improvements.
- Simulate changes to the production line and immediately verify their impact on safety and performance.
Currently available for the Adam human model, RULA enables companies to simulate and improve human-machine interactions, creating a safer and more productive work environment. Thanks to the RULA module and the Adam human model, companies can design workspaces where humans and machines interact safely and efficiently, advancing towards a more balanced and sustainable production model.
The RULA module was developed as part of the CONVERGING project, funded by the European Union. This project aims to address global challenges posed by economic crises and the COVID-19 pandemic. CONVERGING focuses on creating smart, reconfigurable production . Such systems allow autonomous resources, such as collaborative robots, AGVs, and human operators, to work together safely and harmoniously.
In this new paradigm, ergonomics is not just a supplementary consideration but a foundational principle. Adapting production lines to the physical and cognitive needs of human operators reduces the risk of injury but also enhances overall system performance. Thus demonstrating that technology can and should support humans.
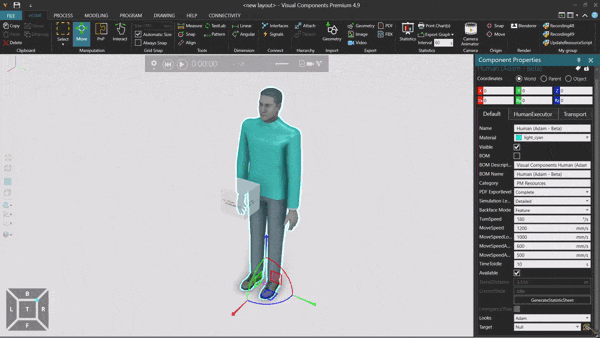
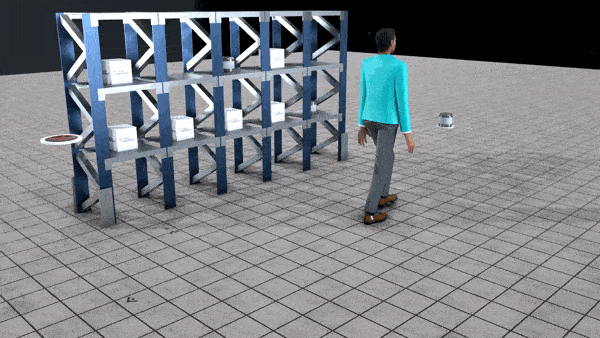
Technology that empowers humans, rather than replacing them
With tools like Visual Components 4.9 and the RULA module, companies can design production lines that optimize human-machine interactions while ensuring operator safety and well-being. The evolution introduced by Industry 5.0 shows that, despite technological advancements, the individual remains central to the production process.
The goal is not to replace humans but to integrate them with technologies that enhance their abilities. This makes the factories of the future not only more efficient but also more human-centric.
Contact Flexcon: learn more about Visual Components and the RULA component.